Background and Situation:
- The ISOM accident of 2005 resulted in extraordinary scrutiny by government and regulatory agencies of the site’s operating procedures.
- The strengths of the site included a sincere desire by management to improve safety and reliability and an overall willingness to change. BP management willing and able to work as a team to address process gaps and drive safety and reliability improvements.
- Some well-documented work processes existed. Improvement did not require a complete re-design of all processes and procedures.
- The work management process was inconsistently executed across the 4 major asset groups in the refinery.
- The work management process was unclear with respect to roles and responsibilities. Managers were unable to effectively implement changes to the process without additional resources.
Objectives:
- Implement consistent planning and scheduling, enabling the site to better control how work is managed and performed.
- Provide a structure work process to assure timely execution of intended maintenance activities.
- Create space for implementing Control of Work activities
- Develop leading and lagging process indicators and the mechanisms to communicate and commit to actions.
- Demonstrate improved control over activities that directly and indirectly affect safety, environmental compliance, availability and costs.
- Support a drive to move site safety to satisfactory levels and initiate an improvement trend to eventually exceed satisfactory levels.
- Drive site availability to satisfactory levels and initiate an improvement trend to eventually exceed satisfactory levels.
Results:
- Control of Work project was implemented on the foundation provided by the implementation of the Work Management process.
- The site now has a consistent Maintenance Work Management process, including a process sustainability and improvement program, that is consistent with a global Maintenance Operating Model for all BP refineries.
- An appropriate set of KPI’s is being generated and utilized to drive process improvements.
- Percent of reactive work decreased from over 40% to less than 10%.
- On-stream Mechanical Availability improved from 80.6% to 86.4%.
- Total annualized savings from availability improvements = $32,651,000
- Achieved bottom-line ROI = 5.0 : 1.0
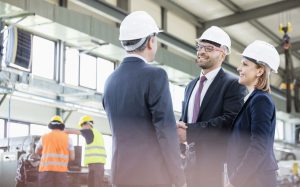